The 3D printing process turns CAD models into physical objects through a layer-by-layer technique. This allows engineers and designers to test prototypes and reduces time to market. Contact By3Design now!
This method is used to produce everything from a plastic cup that supports a mountaineer’s hip implant to cobalt-chrome fuel nozzles that weigh less and are five times stronger than their traditional counterparts. Selecting the right process depends on your application’s needs.
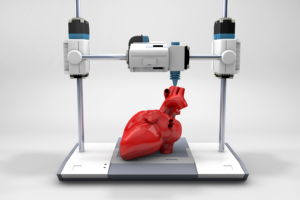
Rapid prototyping is the process of converting computer-aided design (CAD) data into physical models, reducing time and costs associated with traditional production processes like CNC machining or injection molding. It also allows engineers and designers to test out their designs more quickly, making necessary adjustments before moving on to mass production.
Physical prototypes provide a tangible product for stakeholders to assess, encouraging more effective communication and decision-making. Additionally, many of the technologies used for rapid prototyping are more material-efficient than traditional manufacturing methods, resulting in reduced waste. Finally, the ability to develop products faster gives companies a competitive advantage in the market and helps get their innovations to customers sooner.
While there are a number of benefits to Rapid Prototyping, it is important to understand its limitations. The most obvious is that not all rapid prototyping techniques produce parts with the same quality and performance as production-grade materials. This can result in discrepancies between aesthetics and functionality, particularly when using plastics. Additionally, some of the techniques have size constraints that limit the dimensions of the prototypes they can create. Finally, it is important to test prototypes thoroughly to ensure that they are functional and fit for purpose.
Fortunately, there are several different rapid prototyping techniques available to suit the needs of each project. One popular option is waterjet cutting, which uses a high-pressure stream of water, often mixed with abrasive particles, to cut a variety of materials. It is a versatile and cost-effective method for prototyping that can be used in many industries.
Another option is 3D printing, which utilizes a laser to melt layers of material and build up a solid object. This technique is fast and can be used to create complex shapes. It can be used for a wide variety of applications, including industrial design, medical devices, consumer electronics, and architecture.
In addition to allowing engineers and designers to make changes before starting the final product, rapid prototyping can help them find any flaws or defects in their designs. By testing a prototype with the actual material that will be used in production, they can avoid costly mistakes in the final product and reduce the risk of production delays.
Bioprinting
Unlike traditional 3D printing, which uses inkjet technology, which prints pieces of material layer by layer, bioprinting uses inks that contain biological materials. This allows scientists to closely mimic the environments they want to study. These living constructs can be used in everything from drug testing to research on animal models. It could also one day lead to the creation of fully functional organs.
The first step in bioprinting is to create a virtual model of the object that needs to be printed. This may be a CT scan or MRI of a real part, or it can be created from scratch using 3D modeling software. This model acts as a blueprint for the printer to follow. It will help determine the type and amount of material needed for the print. Once the model is created, the bioprinting material can be prepared. It may be a simple solution that will only need to be mixed with the cells, or it may include the actual cells themselves. These solutions are known as bioinks.
Once the bioink is ready, it can be loaded into the 3D printer. Depending on the application, this can be as simple as loading ink into a standard 2D printer. However, when creating cellular applications that require the actual cells to be printed, the process is much more complicated. This can take several weeks, as the cells must be prepared and grown to a large enough size to print.
Once printing is completed, the cells will settle into their new environment. This can be done through a number of different techniques, including using microfluidics, which can manipulate the physical properties of the cell’s environment. It can also be done by introducing chemical cues that are designed to encourage the cells to grow in specific directions.
Some of the most exciting applications of this technology are related to regenerative medicine and personalized medicine. Regenerative medicine aims to help the body heal itself by amplifying or aiding the natural processes that occur in healthy tissue. Personalized medicine is about moving away from the “one-size-fits-all” approach to healthcare and toward treatments that are tailored to each patient.
Medical Technology
Applied to medicine, 3D printing is used in a variety of ways. From prosthetics and artificial joints to replicating organs and internal bodily structures on CT scans in preparation for surgery, to creating cheaper and better-fitting medical tools, the possibilities are endless.
To make an object, a virtual design is made using computer-aided design (CAD) software. The model is then broken down into layers, which are printed one at a time to form the final three-dimensional object. Currently, the most popular type of 3D printer uses a method called fused deposition modeling (FDM). The FDM technique works by extruding heated plastics into thin horizontal layers. The layers are then fused together using heat to create a solid object. This technology is typically the fastest of the three most common techniques.
Once the layer-by-layer fabrication process is complete, medical professionals can use the printed models to improve their understanding of anatomical and pathological structures. They can also use them to practice surgical procedures, and as a tool for patient education. In addition, advances in 3D printing can allow for multi-color and multi-material objects to be printed.
Medical devices are used to prevent, diagnose, monitor and treat diseases or injuries, and they are an essential part of healthcare. From pregnancy tests to ultrasound scanners and x-ray machines, medical technology is with us from birth until death, ensuring that we live longer and more healthily, and keeping our bodies in good working order.
The world’s top medtech companies are constantly developing and testing new products to help improve people’s lives. This is why they reinvest a significant proportion of their revenues into research and development, so they can stay ahead of the competition. As a result, they provide the most advanced diagnostics and treatment solutions, as well as state-of-the-art healthcare facilities and consumer healthcare products like bandages and thermometers. In a globalised and online world, medical technologies can help to connect doctors, hospitals and patients, as well as providing digital tools for monitoring and sharing vital health data. It’s why the medtech industry is a renowned and respected branch of the global economy.
Architecture
A new generation of architects is pushing the boundaries of 3D printing, applying it to a wide range of architectural projects. The technology offers a high degree of customization, allowing architects to create bespoke components and structures that would be impractical or impossible to produce using traditional methods. The technology also provides new opportunities for inventive structural design, allowing architects to produce complex forms of material that are both structurally efficient and visually striking.
In addition, large-scale additive manufacturing can allow architects to create building components that are fully assembled on site, reducing construction costs and minimizing waste. Moreover, digital fabrication techniques allow architects to test their designs for structural integrity and other critical factors before breaking ground. This is particularly important, given the complexity and risk involved in some of today’s largest architectural projects.
Advancements in digital fabrication have made it easier than ever to translate a CAD model into a printable file. Many modern CAD software platforms have dedicated 3D printing modules that streamline the process, though it’s still necessary to perform some basic conversions to ensure that your files are accurate at print scale.
Perhaps the most significant application of 3D printing in architecture is the ability to easily create complex geometries that were previously impossible or extremely challenging to realize. Projects like the VULCAN pavilion by the Laboratory for Creative Design in Beijing illustrate the possibilities of using 3D printing to create fluid, organic shapes that push beyond rectilinear forms and planar surfaces.
The future of 3D printing in architecture looks bright, with continued advancements in both printing techniques and printable materials. As technology evolves, we may see a shift towards hybrid construction methods that combine 3D printed components with traditional construction techniques to improve efficiency and cost savings. We may also see greater automation, allowing buildings to self-assemble and make adjustments based on environmental conditions.